Preliminary Soldering before Housing The good battery core is loaded into the aluminum shell, and spot welding is for the subsequent sealing welding of the top cover and the shell. The top cover and the shell are pre-welded and fixed to prevent the dislocation of the top cover from affecting the quality of the battery. Main control points The shell…
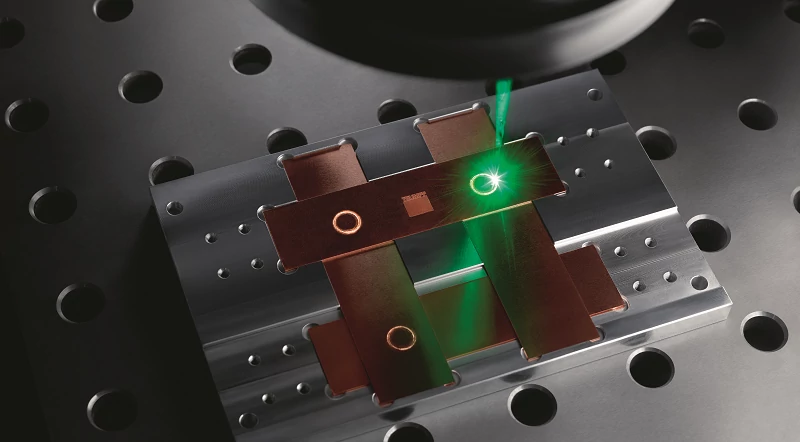